
MAMCO Precision Molding
The current Injection Molding climate is very demanding with a continuous demand from the market to reduce the product price. The pricing as demanded by the market, forces the businesses to reduce product development and manufacturing costs to remain competitive. Manufacturing costs of a product can be broadly categorized in the following heads:
• Raw material
• Labor
• Process that is technology driven
Product engineers are constantly faced with the following challenges:
• Reduce production cost
• Reduce the material cost
The MAMCO Value Analysis & Value Engineering (VAVE) methods are very important and useful in driving down the product cost which helps companies retain market share and sustain their profitability. Understanding how conditions effect your production process is important. Great understanding of that process and the machines, material and people required to deliver your product is critical.
​
​
Injection Molding
Injection molding is a manufacturing process for producing parts by injecting molten material into a mold. Injection molding can be performed with a host of materials mainly including plastics, metals (for which the process is called die-casting), glasses, elastomers, confections, and most commonly thermoplastic and thermosetting polymers. Material for the part is fed into a heated barrel, mixed (Using a helical shaped screw), and injected (Forced) into a mold cavity where it cools and hardens to the configuration of the cavity.

What Goes into your Project
​
Injection molding uses a ram or screw-type plunger to force molten plastic material into a mold cavity; this solidifies into a shape that has conformed to the contour of the mold. It is most commonly used to process both thermoplastic and thermosetting polymers, with the volume used of the former being considerably higher. Thermoplastics are prevalent due to characteristics that make them highly suitable for injection molding, such as the ability to soften and flow on heating. Thermoplastics also have an element of safety over thermosets; if a thermosetting polymer is not ejected from the injection barrel in a timely manner, chemical crosslinking may occur causing the screw and check valves to seize potentially damaging the injection molding machine.
​
When thermoplastics are molded, typically pelletised raw material is fed through a hopper into a heated barrel with a reciprocating screw. Upon entrance to the barrel, the temperature increases and the Van der Waals forces that resist relative flow of individual chains are weakened as a result of increased space between molecules at higher thermal energy states. This process reduces its viscosity, which enables the polymer to flow with the driving force of the injection unit. The screw delivers the raw material forward, mixes and homogenizes the thermal and viscous distributions of the polymer, and reduces the required heating time by mechanically shearing the material and adding a significant amount of frictional heating to the polymer. The material feeds forward through a check valve and collects at the front of the screw into a volume known as a shot. A shot is the volume of material that is used to fill the mold cavity, compensate for shrinkage, and provide a cushion (approximately 10% of the total shot volume, which remains in the barrel and prevents the screw from bottoming out) to transfer pressure from the screw to the mold cavity. When enough material has gathered, the material is forced at high pressure and velocity into the part forming cavity. The exact amount of shrinkage is a function of the resin being used, and can be relatively predictable. To prevent spikes in pressure, the process normally uses a transfer position corresponding to a 95–98% full cavity where the screw shifts from a constant velocity to a constant pressure control. Often injection times are well under 1 second. Once the screw reaches the transfer position the packing pressure is applied, which completes mold filling and compensates for thermal shrinkage, which is quite high for thermoplastics relative to many other materials. The packing pressure is applied until the gate (cavity entrance) solidifies. Due to its small size, the gate is normally the first place to solidify through its entire thickness. Once the gate solidifies, no more material can enter the cavity; accordingly, the screw reciprocates and acquires material for the next cycle while the material within the mold cools so that it can be ejected and be dimensionally stable. This cooling duration is dramatically reduced by the use of cooling lines circulating water or oil from an external temperature controller. Once the required temperature has been achieved, the mold opens and an array of pins, sleeves, strippers, etc. are driven forward to demold the article. Then, the mold closes and the process is repeated.
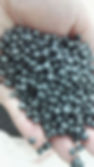

Material
​
Most polymers, sometimes referred to as resins, may be used, including all thermoplastics, some thermosets, and some elastomers. Since 1995, the total number of available materials for injection molding has increased at a rate of 750 per year; there were approximately 18,000 materials available when that trend began. Available materials include alloys or blends of previously developed materials, so product designers can choose the material with the best set of properties from a vast selection. Major criteria for selection of a material are the strength and function required for the final part, as well as the cost, but also each material has different parameters for molding that must be taken into account. 6 Other considerations when choosing an injection molding material include flexural modulus of elasticity, or the degree to which a material can be bent without damage, as well as heat deflection and water absorption. Common polymers like epoxy and phenolic are examples of thermosetting plastics while nylon, polyethylene, and polystyrene are thermoplastic.
